When aquifers underlay made ground a stone column is sometimes perceived as potential path for contamination. In reality, vibro treatment reduces the mass permeability and so this is rarely an issue. However, in some cases it is necessary to seal the base of the columns. This is where Keller’s Environmental Stone Columns (ESC) can provide the perfect answer. In the long term developments such as retail parks and supermarkets are covered with hard standing and this surfacing and the buildings are effectively a barrier to downward percolation of surface water.
Keller can mitigate this risk by installing ESCs. ESCs have a minimum one metre thick lean mix concrete or grout plug at their base installed with a modified bottom feed vibro rig. This technique prevents contact of the stone part of the column with any permeable stratum which could be an aquifer but allows the benefits of vibro to be taken advantage of.
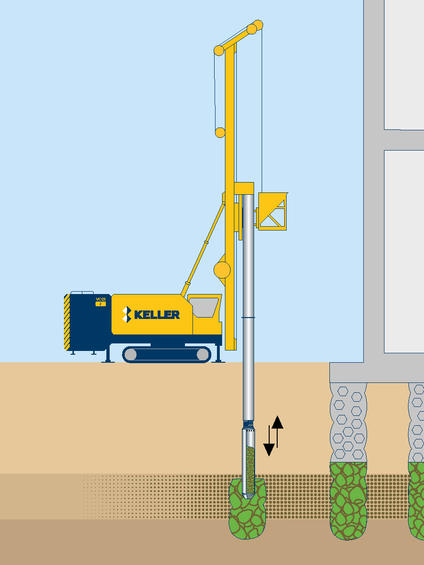
Common uses
Process
In the bottom-feed vibro process, the vibrator penetrates to the design depth using the vibrator’s weight and vibrations, as well as air jets located in the tip. Either a concrete plug is pumped or the stone is added. When grouted ESCs are formed the lower part of the column is then grouted and the column built above in the normal way.
Vibro rigs are fully instrumented with an on-board data acquisition system to ensure the correct level of the impermeable plug relative to the aquifer or permeable stratum to be protected. Data from the system, such as amperage and lift rate, can then be recorded and displayed in real-time alongside specified target values on an in-cab monitor. This monitoring allows the operator to correct any deviations in real-time during the construction process to keep the vibro compaction within project specifications.
Specialist Contact | Rob Herring - [email protected] - +44 (0)7767 446830
Advantages
Quality assurance
The vibro equipment we use is designed and manufactured by our in-house equipment manufacturer exclusively for use by Keller companies.
In-house quality production management software enables us to capture and analyse data in real time and validate the performance of the ground improvement being carried out.
A variety of production parameters are generally logged during execution including depth, current, pull down force, uplift/pull down sequence, time and date and element number.
Field trials can also be used to verify column production parameters, along with static load tests, single or group, column material compressive strength tests, and column diameter verification.